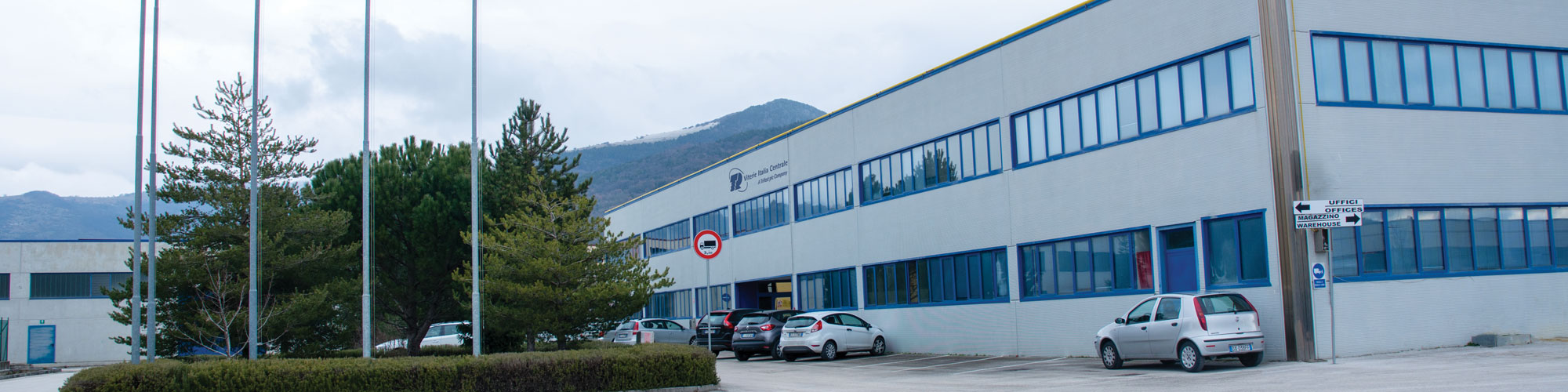
TR VIC – a renowned manufacturer
Credit: Will Lowry, Fastener + Fixing Magazine
22.09.2023
Share this article
TR VIC (Viterie Italia Centrale SpA) has been manufacturing fasteners in Fossato Umbria for over 50 years and is one of the most renowned manufacturers in Italy – with a history of product development and innovative design capability.
From its Italian site, TR VIC manufactures products for many well known global brands and distributes the products to multiple customer locations across four continents – becoming recognised for male threaded cold forged products, specifically to customer drawings, and in the development of products to enhance production assembly methods.
TR Fastenings, the parent company of TR VIC, was historically known as being a provider of fasteners to the electronics and tech industries and over the last 15 years its focus has diversified into the automotive sector – becoming a key supplier to tier 1 companies. To retain a balanced customer spread, TR Fastenings also focused on the health and home sector, which encompassed domestic appliances, and was already supplying this sector to a smaller degree before the acquisition of VIC gave it a much larger market share.
Another important reason for the acquisition of TR VIC, was the advantage of having a manufacturing facility in ‘middle Europe’ that could meet the needs for faster prototyping and shorten lead times compared to Asia supply. TR already had five manufacturing sites in Singapore, Malaysia, and Taiwan, and this acquisition significantly increased its manufacturing capability and footprint.
Inevitably, existing customers showed an interest in having a TR manufacturer in Europe and when TR VIC gained the IATF16949 accreditation it opened up further opportunities. TR VIC management also embarked upon an investment program that included a state of the art heat treatment plant; new automatic packaging machines; and the upgrading of machinery and facilities. This culminated in a recent £5 million (€5.8million) investment to increase TR VIC’s manufacturing footprint by 30%, by adding new forging, thread rolling and pointing machines. This included the addition of 6-die 6-blow machines from Carlo Salvi and SACMA Group, which has increased the diameter range TR VIC is able to produce. The growing portfolio of machinery also increases TR VIC’s capacity, especially for more complex applications within the sectors that it services.
Investments to the manufacturing location; a focus on environmental improvements; and a major facelift of the offices; has ensured that TR VIC is seen as a modern facility that is appealing to a discerning customer base. Additionally, the company has developed further warehouse capacity capable of holding 12,000 pallets. Plus, investment in training, initiated by Stefano Pisoni, managing director of TR VIC, has developed into a formal training academy, which has become key to recruitment and staff retention – with the headcount since acquisition almost doubling.
Investment in people, capability, and capacity, is key and never more so than during the Covid-19 pandemic. The huge increase in requirements for domestic appliances put a strain on the team at TR VIC, but they met the challenge. This significant increase in demand was driven by people working from home during lockdowns, investing in new appliances, lifestyle products and making home improvements. This societal transformation meets with a rapid deployment of new technology to improve quality of life, from fresh ground coffee machines to clean air products and personal grooming, all of which have rich fastener content.
Innovation is key
Another fundamental aspect of TR VIC’s success has been innovation, with the company winning several design awards, including the TR EPW screw for thin sheet metal, which picked up the Route to Fastener Innovation 2019 award at the Fastener Fair Global show. The transit fasteners for washing machines and tumble driers were also a design success some years ago – reducing four components to a combined recyclable component, which is still in high demand.
Another aspect is meeting the needs of the market, such as the new European legislation ‘Right to Repair’ which came into force last year. This is already changing assembly methods as there is a move away from welded products to fasteners that can allow for disassembly. TR VIC is working with global brands who are focused on returning to core conventional fastener methods.
This is a very positive development that has been years in the making. While this is primarily about giving control back to the consumer, this is also a very strong environmental improvement case. It will significantly reduce appliances destined for landfill, which can now be repaired.
Another example would be a high volume part for an automotive lighting cluster assembly – where TR VIC produces 60 million pieces a year. The current part features a neoprene washer under the head of the screw to prevent water ingress. However, TR VIC has designed in a special screw, which it has patented, that has a unique feature under the head that negates the need for the washer. This has improved the integrity of the product, time to manufacture and has given a cost and recyclable environmental benefit to the customer.
TR VIC’s approach to sustainability is also highlighted in the cleaning of products through to researching environmentally friendly packaging materials, as well as the movement of product between manufacturing areas. This investment is seeing real benefits for TR with keen interest in the TR VIC facility shown by numerous customers, with nine audits taking place in the next two months. Due to geopolitical issues in other parts of the world, TR is also experiencing a high demand from customers to ‘near shore’ their product. The introduction of CBAM will also accelerate the need for products to be manufactured in Europe and therefore further investment to increase capacity is inevitable. Enhancing the technical support that the company can give to customers at the early design stages is crucial for the future.
For instance, the EV and EVB opportunities are an interesting example of new product for this growth industry. To meet new product requirements, TR VIC has invested heavily in developing product forged in copper, which will be a real game changer. “Supporting customer requests, particularly in emerging technologies is key to our future,” explains Andrew Nuttall, managing director for TR Europe and the UK. “Working together in these developments we can achieve our respective objectives and future proof our business.”
Supporting customer requests, particularly in emerging technologies is key to our future. Working together in these developments we can achieve our respective objectives and future proof our business.