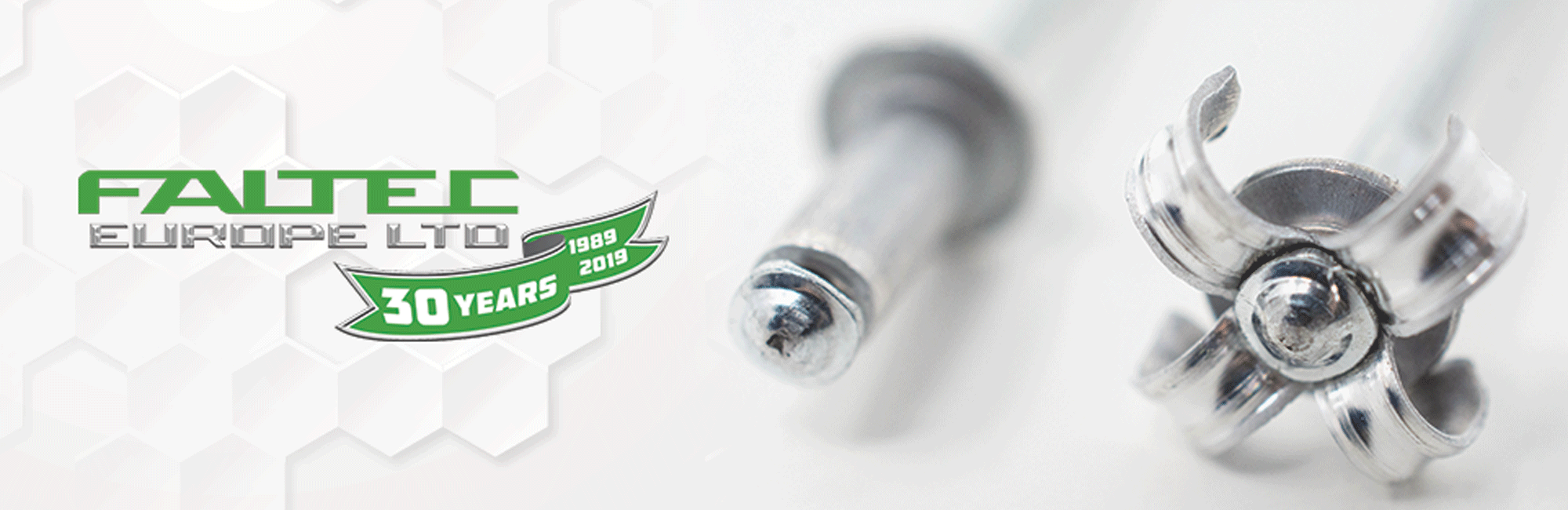
TR Fastenings provides bespoke fastening solution to leading Tier 1 automotive company
12.02.2020
Share this article
Faltec Europe employs TR Fastenings to deliver competitive fastener supply and tooling solution
About Faltec Europe
Faltec Europe Ltd, part of the global Faltec Group, is a world-class manufacturing company and an accredited Tier 1 supplier to the automotive sector. Faltec Europe manufacture many of the interior and exterior vehicle trim products you see every day on the most popular cars on UK roads.
Faltec’s European division produces over 300 car products from front bumpers to radiator grills, roof mouldings, door mouldings, door sashes, roof finishers, weather strips and lots more.
Faltec’s business model is based on being robust, flexible and adaptable to meet customers’ requirements within a fast-changing market and global economy. This case study is a true demonstration of that ethos.
Industry landscape
The automotive industry is a vital part of the UK economy. The industry has an £82 billion turnover (plus £20.2 billion value added). More than 30 vehicle manufacturers in the UK rely on a complex network of suppliers - a single car has around 30,000 parts. In the UK there are also around 2,600 component manufacturers supplying parts directly to OEMs.
The automotive industry has a traditional tiered supply chain (Tiers 1, 2 and 3, with Tier 1 feeding directly into OEMs), but some lower tiered component manufacturers, such as TR Fastenings (TRF), are challenging the existing market structure, taking a much larger role in innovation and Tier 1 production-line support.
Project background
Faltec Europe required a bespoke fastening for a new major programme it had recently secured with a key global OEM. The trim product to be developed was an injection moulded exterior trim part for a new vehicle due for release in November 2019.
A late design change to improve the fit of the part to the vehicle required the attachment of a strengthening support via a Peel Type Rivet. Peel Rivets are a type of Blind Rivet designed to offer improved support in brittle, soft or ductile materials, applicable to the vehicle trim products in this project.
Fired using bespoke tooling, the head of the Peel Rivets explode and become mushroom-shaped as they enter the moulding. This creates a large blindside bearing surface, significantly reducing the risk of the rivet sinking into or breaking the moulding.
TR Fastenings (TR) and Faltec are both active within the North East Automotive Alliance (NEAA) network. Following a successful pitch, TR Fastenings was appointed By Faltec as the company’s provider.
TR Fastenings (TR) and Faltec are both active within the North East Automotive Alliance (NEAA) network. Following a successful pitch, TR Fastenings was appointed By Faltec as the company’s provider.
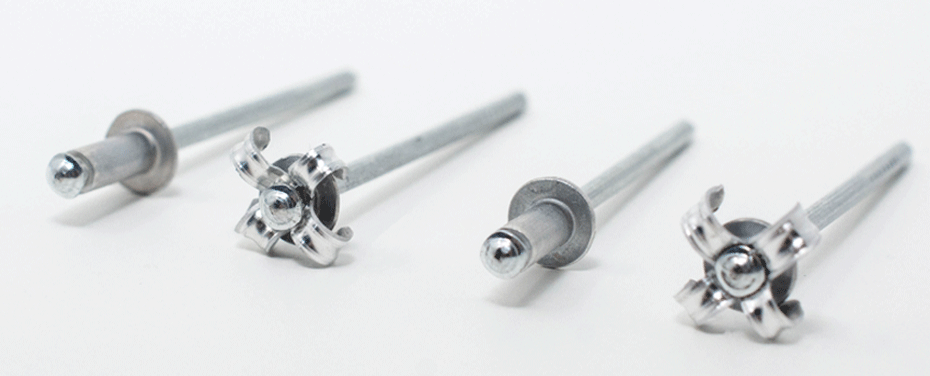
Approach and solution
As a global specialist in the design, engineering, manufacture and distribution of high quality industrial and Cat C fastenings, TR was able to identify the original equipment source and submit a competitive supply solution. TR is renowned for working with clients from design table to production line to achieve innovative, effective and efficient solutions. The TR product and tooling for this project offered a robust solution and would guarantee efficient production - this secured the initial business.
Not only could TR provide the specific fastener solution, but in this instance, it was also able to supply bespoke tooling compatible for the fastener. The tooling required a bespoke rivet gun that would not only automatically fire the rivets into the moulding to be joined, but also have capability to apply rivets in a fast production environment.
Project challenges
Timescales were challenging for both parties but with close co-operation qualified parts were supplied along with tooling for development and ongoing production, both being delivered on time. Not only did TRF have to supply production intent rivets in a short timescale but also the gun was ordered late due to last-minute design changes, requiring 24 hour delivery.
The late design change by the OEM required special rapid response by TR and Faltec. TR was able to take the lead on supplying fast-production intent rivets and tooling in a very short period.
Perhaps the biggest challenge came with technical advice and training. TR had to ensure correct and safe operation of the rivet gun. Due to its bespoke nature, Faltec staff responsible for the operation had no experience in the use of this particular tool and engineering.
Greg further explained that when Faltec first tried the application they thought it had failed. However, once it had been confirmed that the rivet was in fact the correct specification, it was understood that perhaps further assistance would be required in how to use the tool and rivets in a fast production environment.
TR’s Quality Manager, Dave Fearon, visited Faltec at the production facility to help lay out the process and demonstrate how to use the Rivet Tool in a safe manner. It was acknowledged that without correct use, the application could have been dangerous to operators.
As full service was of the utmost importance to TR their engineers visited Faltec several times, initially to explain how the rivet gun would operate, but then to train staff in appropriate use and safety.
TR provided ongoing support throughout the initial trial phase and was asked to assist in technical evaluation ready for onsite production at Faltec. This project is indicative of TR’s service which goes far beyond product supply and applications.
Project outcomes and advantages
TR provided ongoing support throughout the initial trial phase and was asked to assist in technical evaluation ready for onsite production at Faltec. This project is indicative of TR’s service which goes far beyond product supply and applications.
Following success with this project, TR has been nominated to supply serial production, cementing its ongoing relationship with Faltec.
Outcomes and advantages of the project included:
- Parts and tooling were delivered on specification and on time given challenging timescales
- Due to TR’s extensive capability, it was able to offer Faltec additional product tooling over and above the initial bespoke fastening RFQ
- TR provided ongoing project support ensuring onsite production timescales were met
- The successful project has resulted in ongoing work for TR for the supply of serial production for a further three years
Project reflections
TR provided ongoing support throughout the initial trial phase and was asked to assist in technical evaluation ready for onsite production at Faltec. This project is indicative of TR’s service which goes far beyond product supply and applications.
Related articles:
- North East Automotive Alliance (NEAA) Case Study - TR Fastenings Provides Bespoke Fastening to Leading Tier 1 Automotive Company
- International Sheet Metal Review - 'Faltec case study' - February 2020 - Page 31
- Torque Expo - 'What’s new in rivets and rivet tools?' - 06.03.2020
- Design, Products & Applications – ‘TR Fastenings provides bespoke fastening solution to Tier 1 automotive company’, pages 22 & 23 - April 2020
- FastFixTechnology.com - 'TR Fastenings provides fastening solution to tier 1 company' - 28.04.2020
- Electronics World - 'Fastening solutions for automotive use' - 17.06.2020