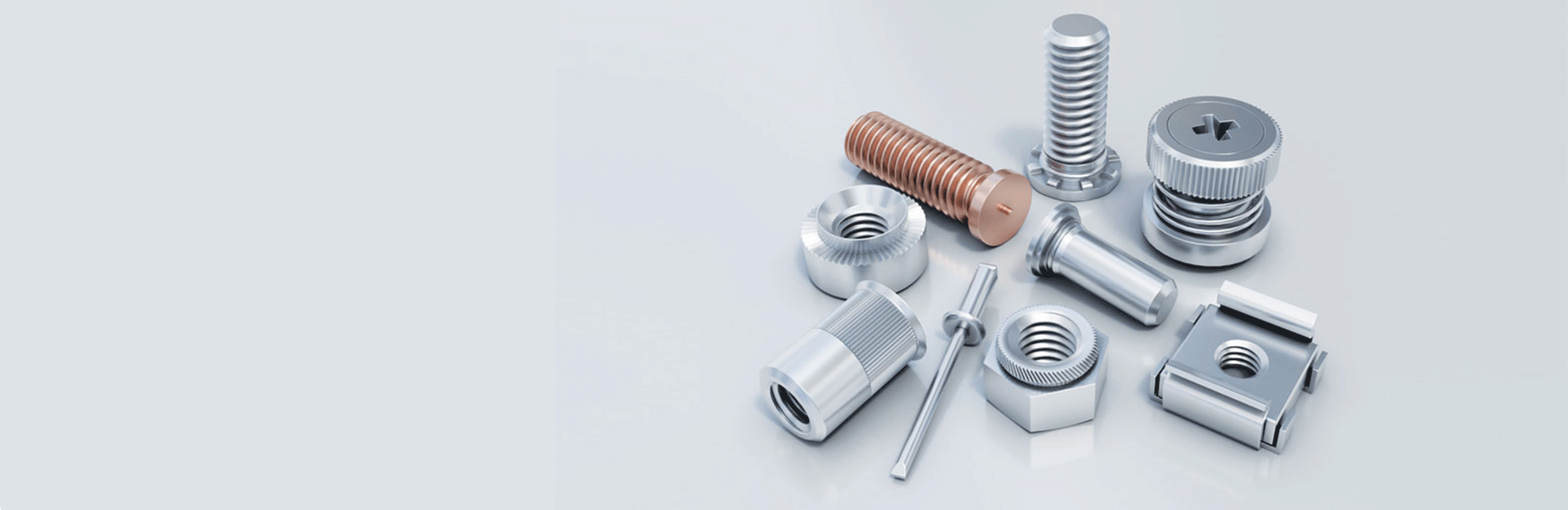
Tightening the fastener choice for Sheet Metal
07.05.2021
Share this article
There are as many joining methods as there are Sheet Metal applications. Selecting the best fastener for an application might not be the best fastener for assembly or disassembly. In most cases fasteners are selected based on a range of factors including physical performance, designers experience with a technology, used installation methods within the manufacturing environment, available sizes and lengths as well as piece price and overall cost.
The most recognizable method of joining two parts together would be with bolt and nut connections. Bolt-nut connections are generally used for detachable mounting of components and sheet metal parts. A nut is retained based on creating sufficient friction within the thread and between the interfaces of the fastener and Sheet Metal. The preload is created by stretching the bolt during tightening up. A relatively longer bolt can stretch more than a short bolt and is therefore better capable in retaining a nut by friction alone. Because of this, standard nuts and bolts are not always the best solution for joining Sheet Metal.
There are multiple methods to improving the retention of nuts onto bolts, such as the application of polymeric patches on the screw, which fills the cavities between the two mating threads. Similarly, a Nylon Ring attached to the nut will provide a light interference between the thread and the polymer. Other options can be mechanical deformation of the nut or thread to increase pressure within the thread. The retention does not address the function of the joint. Most bolted joints are designed to be friction-grip joints: the preload in the bolt presses the Sheet Metal components together with such a magnitude that the friction between the components is enough to withstand forces along the Sheet Metal. If the forces along the metal sheets exceed the friction forces, the joint will slip, and the bolted joint will be subjected to shear forces. Henceforth the joint becoming practically a shear joint.
Accurate tightening and creating of pre-load functions better with longer than with shorter bolts and is therefore more suited in heavy laden dynamic applications with components with greater thickness.
Lockbolts
Can be a permanent solution if joints are not subject to maintenance. A metal ring is squeezed around a pin with helical or annular grooves, thereby providing a continuous pre-load.
The fasteners do however need access from both sides. Single sided access can improve assembly efficiency or even might be a requirement due to difficulty to reach both sides of the application.
Blind Rivets
Have been specifically designed to allow single sided access. Most designs are based on applying tension to an integrated or reusable mandrel, which increases the body diameter on the blind side by splitting, bulbing or expansion.
Compared to nut and bolt joints, blind rivets provide a lower pre-load. Therefore, blind rivets are mainly used as shear joints. Some blind rivets have the additional benefi t of being hole filling, increasing joint integrity.
Blind Rivet Nuts and Studs
Can be used as a hybrid solution, whereby the rivet part either fits in a single-layer component or joins multiple layers together. The addition of a metric thread, either as stud or nut, enables further metal sheets or components to be joined with respectively a nut or screw.
The concept of Blind Rivets can be found in the use of Solid Rivets, where one side of the fastener is deformed using an anvil or die when the fastener has been placed in the hole. Solid Rivets do therefore need access from both sides and through-holes in the sheet metal.
Self-piercing Rivets are a variant on this subject, where a cup shaped, hardened rivet is pushed into the metal. The hardened rivet deforms the layers of sheet metal and forms an interference joint. Generally, a die is used on the blind side to create a mating profile. In certain materials, such as aluminum, it is possible to set the fasteners without the use of a blind side die. The benefit of this method is the possibility to automate assembly without the need of preparing the joints with holes to fit the fasteners.
Developing products for a ‘circular economy’ finds its fundamentals in developing products with an extended economic life span and are then suitable for re-use, repurpose or recycling at minimum cost and maximum effienciency and retention of value. This does place again emphasis on the use of reversible threaded fasteners, allowing reuse of parts during repair and maintenance and easy recovery of individual parts when the application is dismantled.
As was earlier established the use of bolts and nuts have the benefit of being removable, but require access from both sides, unless either part has a pre-fitted nut or male threaded part. Cage Nuts and Captive Screws are well-known examples. The nuts can be clipped into square holes and are often used to compensate for some misalignment in joints.
One option is to attach the male threaded part to one of the components. This can be done either by welding or clinching. Weld studs can be manually or fully automatically placed and have an aesthetic benefit of being (nearly) invisible from the blind side, because no part will protrude. A downside is that parts have to be welded before coating or painting and generally the stud and component material have to be similar to allow welding. If double sided access is possible before assembly, studs could be fitted to the component by clinching. Self-Clinching studs do require a pre-punched hole, but the stud to be of a dissimilar material to the component material. All parts can also be pre-painted or coated. Instead of fitting a male fastener part to the component, it is possible to pre-fit a nut. This can also be done using self-clinching products such as the K-Series® Nut. Alternatively, Self-piercing Nuts or Weld Nuts are an option.
Eventually, it might be possible to remove the nut completely and fit a screw directly into the sheet material. With a preference for isometric threads, it can be possible to cut, punch or laser a hole or deep drawn a collar, which can then be tapped with a thread. Doing this requires additional operations during the manufacturing of the individual components adding to cost.
The use of Thread Forming or Cutting Screws removes the need of creating a screw thread in the counter parts, reducing number of operations, part numbers and overall cost. Some methods require a pilot hole, where other types of screws can be installed directly into the sheet metal without the need of a hole. Self-drilling Screws are equipped with a drill bit shaped point which creates a hole into which the thread is formed. Even though not requiring a hole for installation is attractive, formation of swarf limits the use in mass production environments.
Flow Drilling and Fllow Forming Screws are also equipped with a special tip, but instead of drilling, it is designed to melt the material locally to allow the sheet material to flow and a mating thread to be formed by the screw. The joint will be resilient against vibrational loosening due to intimate mating of the threads. Flow Drilling Screws do require robotic installation and high installation speeds, whereas flow forming, such as the TR EPW screws can be installed manually.
Equipping parts with pilot holes or pre-extruded holes, Thread Forming Screws can be used. These can either be fitted with a thread forming tip or have a trilobular design, which aids thread rolling. These types of fasteners are used extensively in automotive and other high-volume assembly lines. The benefit of this type of screws is the adherence to a metric thread form, allowing the fastener to be replaced by a standard metric screw in case of repair and maintenance.
TR Clinch Nut Installation:
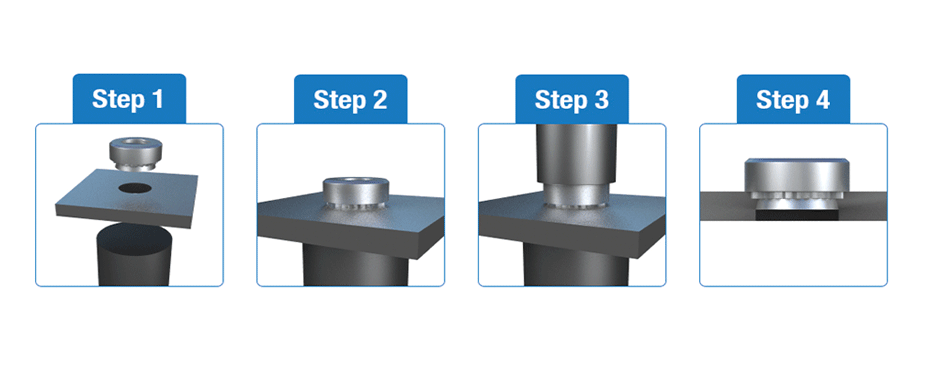
- Materials and thickness to be joined – is it possible to standardise?
- Strength of the connection and type of joint – torque tightening or shear joint?
- Corrosion resistance – do materials suit together or is there chance of galvanic corrosion?
- Accessibility – can the joint be reached from both sides or would single sided access be required or beneficial?
- Automation – are the fasteners to be installed automatically to cope with high volumes?
- Takt time – not every fastener installs at the same speed.
- Poka-yoke – ensure that the correct fastener is used in the correct joint.
Credit: Institute of Sheet Metal Engineering