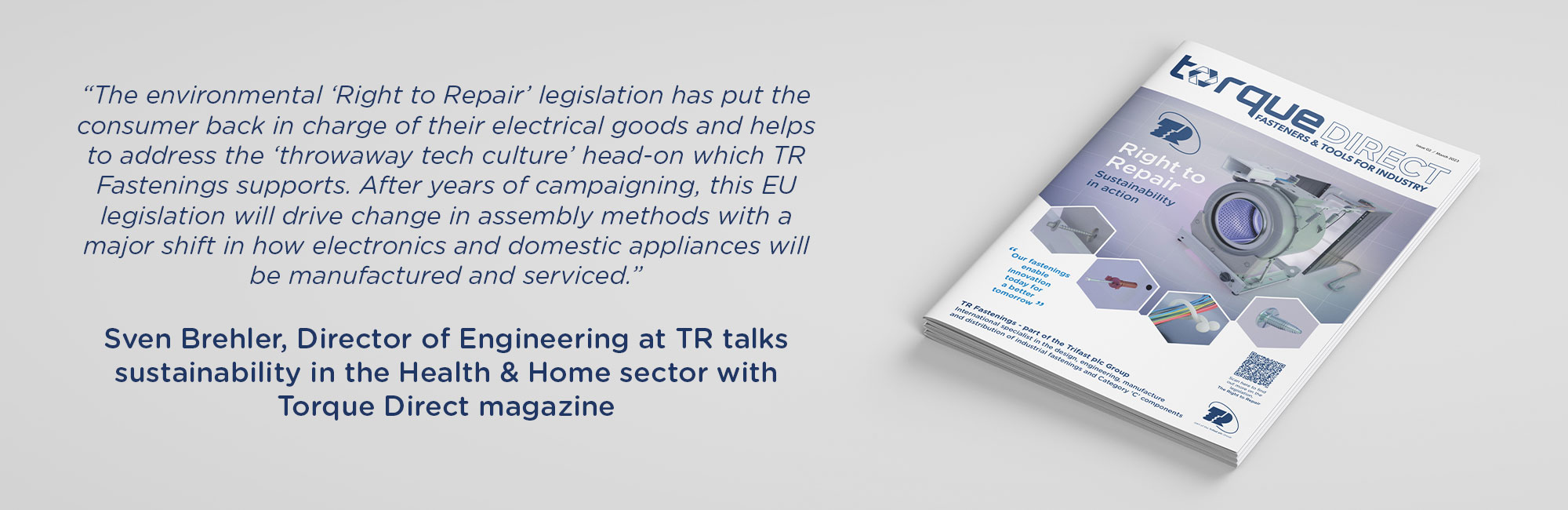
Sustainability into Action
Sven Brehler, Director of Engineering and member of Trifast plc ESG Committee
28.03.2023
Share this article
As a major fastener supplier to the Health and Home sector TR is actively supporting new designs and the re-introduction of fasteners that can be accessible for disassembly and repair.
For us as consumers of household goods we have got used to more limited life span of appliances compared to say 30 years ago. Product then, was more solidly built and was assembled by conventional methods using the welding and riveting production methods used less often today. They were however not as aesthetically pleasing, the choice of colours was either cream or white, but they lasted for years. They could also be accessed and repaired quickly with spares readily available, as there were also fewer models available with common parts.
We have come a long way in the design of products to meet our requirements for modern appliances in our sleek kitchens and utility rooms. What has been sacrificed over time is the durability and longevity of the product which inevitably means that product cannot easily be repaired in or out of warranty, and then ends up as scrap and potentially in landfill sites. If it can be repaired, but is out of warranty, it is often too expensive and there is a tendency to replace rather than repair. You could deduce that there is built in obsolescence in the way product is currently manufactured today. It would be better for the environment, and our wallets, if products could return to having the ability to replace components with a screwdriver or wrench and buy spare parts easily. Once a product has been welded or riveted it is nigh impossible to do that. Another case in point would be electrical waste which could be reduced if replacement parts were readily available, and not just to costly service engineers. Well known global brands of vacuum cleaners and electrical garden equipment are starting to enable consumers to buy online battery replacements which is a move in the right direction.
" The environmental ‘Right to Repair’ legislation has put the consumer back in charge of their electrical goods and helps to address the ‘throwaway tech culture’ head-on which TR Fastenings supports. After years of campaigning, this EU legislation will drive change in assembly methods with a major shift in how electronics and domestic appliances will be manufactured and serviced. It is already playing a key role in helping to extend product life, cut carbon emissions, and reduce landfill. Where there are more mechanical assembly methods employed there could even be a boost to create more jobs within the industry sector. "
One example to illustrate the changes that can be consciously made is in the assembly of a washing machine. Working in collaboration with domestic appliance customers this is being urgently addressed. It is clear to see in the washing machine animation which we have produced in house, the return to conventional assembly methods that is being encompassed in the latest designs. A good example would be the move to thread forming screws and high strength fasteners that allow for disassembly and reusability.
Sustainability case study
One example, the transit bolt, can be clearly seen in our washing machine animation. This transit bolt used to be a 5-piece assembly holding the drum securely in transit when it was delivered to your home. Originally this assembly comprised of two plastic spacers, a rubber damper, a metal washer and a bolt which were then discarded once the machine was located in position. TR developed in our Italian manufacturing facility TR VIC, a one-piece assembly that is patented and fully recyclable.
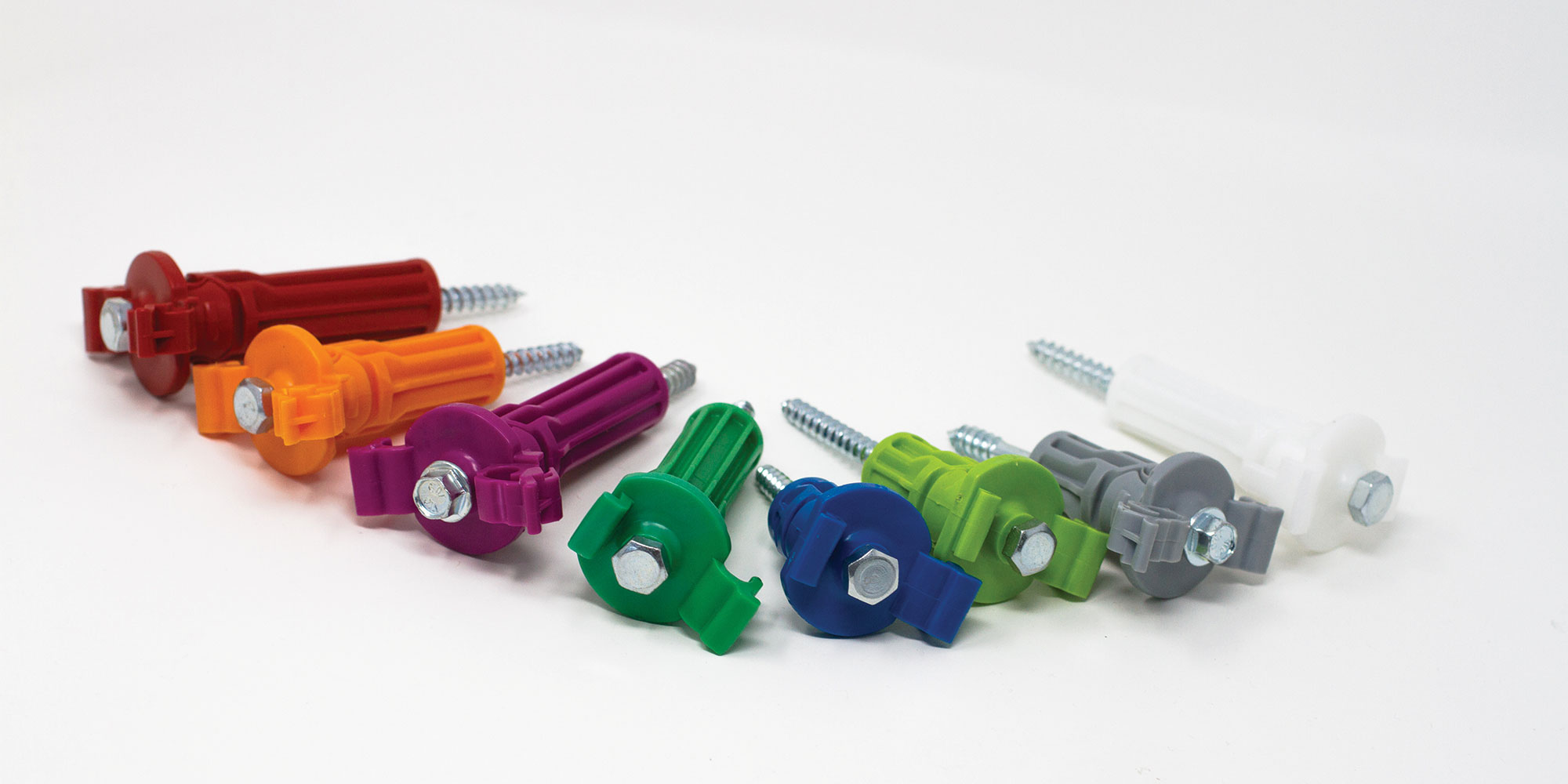
Pictured: TR Transit Bolts
TR Hungary case study
TR‘s Sustainability Report is published on our website. The challenge is to embed this strategy /ethos in a practical way within our business. Last year we opened a sizeable new build location in Hungary. It is not often that you get the chance to design a building from scratch. Our Teams used this opportunity to ensure this building was environmentally compliant, incorporating many features such as solar panels, triple glazed windows, clean air filtration systems in the warehouse, sustainably sourced office furniture and EV charging points. Company vehicles are now all electric. Read the full article on our website.
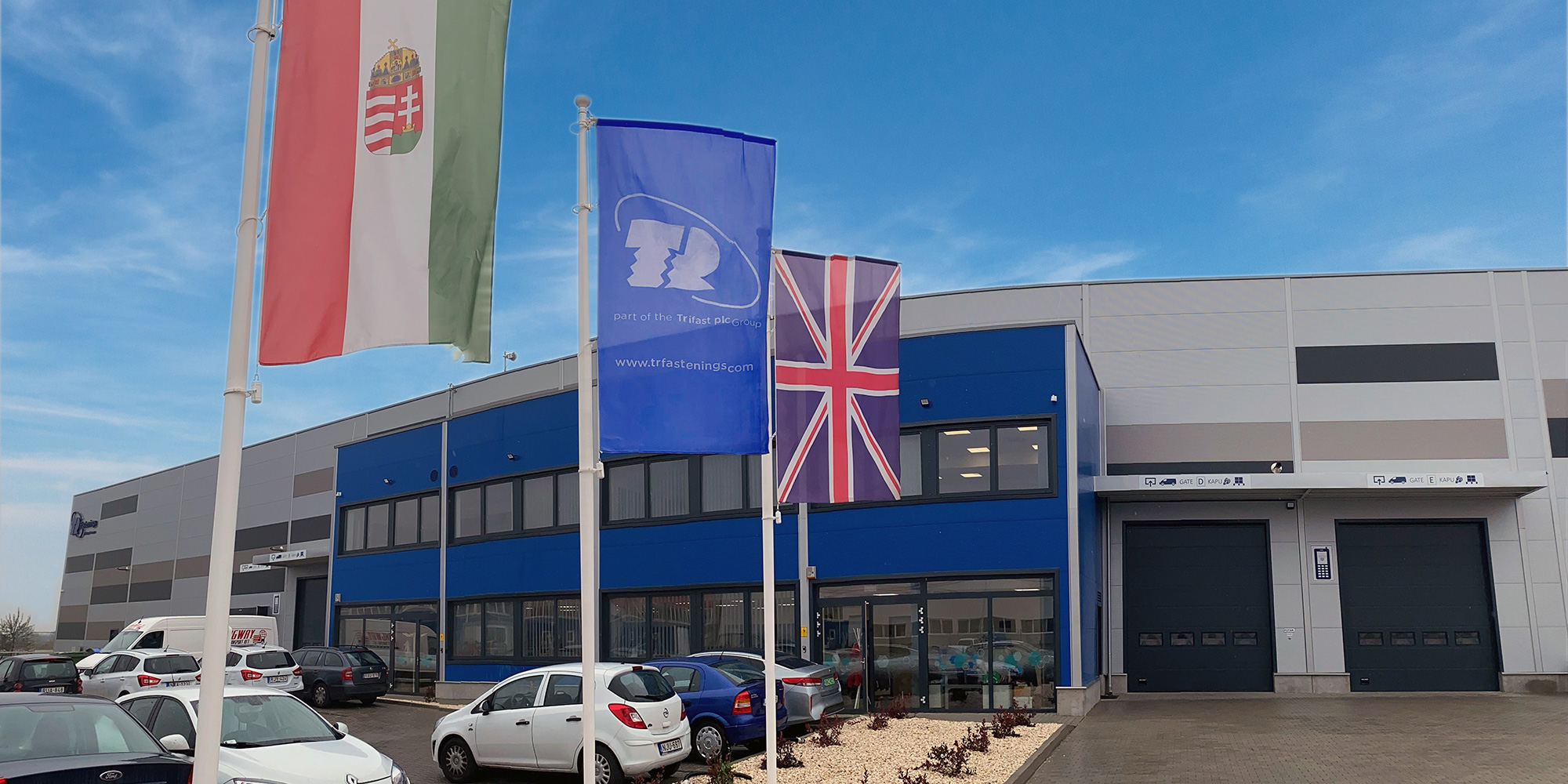
Pictured: TR Hungary
TR VIC Italy case study
This TR manufacturing location is a key supplier to the Domestic Appliance market. The collaboration with the European multinationals and their design and technical teams has been focussed on ensuring that the ‘Right to Repair’ legislation is being embraced and incorporated in all new models. We have taken the same approach in our manufacturing facility in Umbria based on the principal of working towards being Industry 4.0 compliant. This has enabled us to develop a modern, and greener and more efficient workplace. The investment made has been sizeable over the last 5 years culminating in a newly extended production facility and warehouse, new multistage forging machines being delivered, and the work does not end there. This investment increases our production capability by 33% to meet the demands of customers requiring ‘near shoring’ which again is a sustainable target for many companies’ intent on reducing Co2 emissions. There is a never-ending continuous improvement program in place working on reducing waste, oil reclamation and new extraction and filtration systems. Read the full article on our website.
" There is talk that the ‘Right to Repair’ is gathering strength in other sectors too including automotive. "