TR Fastenings designs a unique push screw solution for monitor mounting brackets
19.06.2023
Share this article
In the changing world of home working, hot desking and the need for two screen displays we are seeing changes in how devices are being positioned in the workspace. One global monitor manufacturer whom we have worked with for over 20 years had a requirement for a small but strong fixing solution that enabled easier assembly.
The requirement
The customer, a globally recognised computer and enclosure manufacturer, required a bespoke solution to launch a new product as well as enhance its range of mini-PC screen stands. It first approached TR to help it create more effective fasteners for its mounting brackets when they could not find a solution to attach a stand that would be reusable. It also needed to be capable of screwing and unscrewing repeatedly without wearing or loosening. And it had to be strong enough to take the load and support of the monitor weight.
After consultation with TR, it became clear that it needed a product that was unique for its new launch, something that would go beyond what was currently available in the market.
The solution
The customer had initially set about identifying a plastic rivet solution, but it became apparent that to achieve their goals, a specifically designed component was required. TR’s design and engineering teams supported the request and were able to develop a unique proposition - an innovative and effective push screw rivet.
Together they identified the need to have an insertion force of 35N, to prevent RSI, an extraction force of a minimum of 90N, in order to remain secure, and the need for it to be unscrewed repeatedly with a screwdriver without wearing down over time. No small challenge for a small fastener!
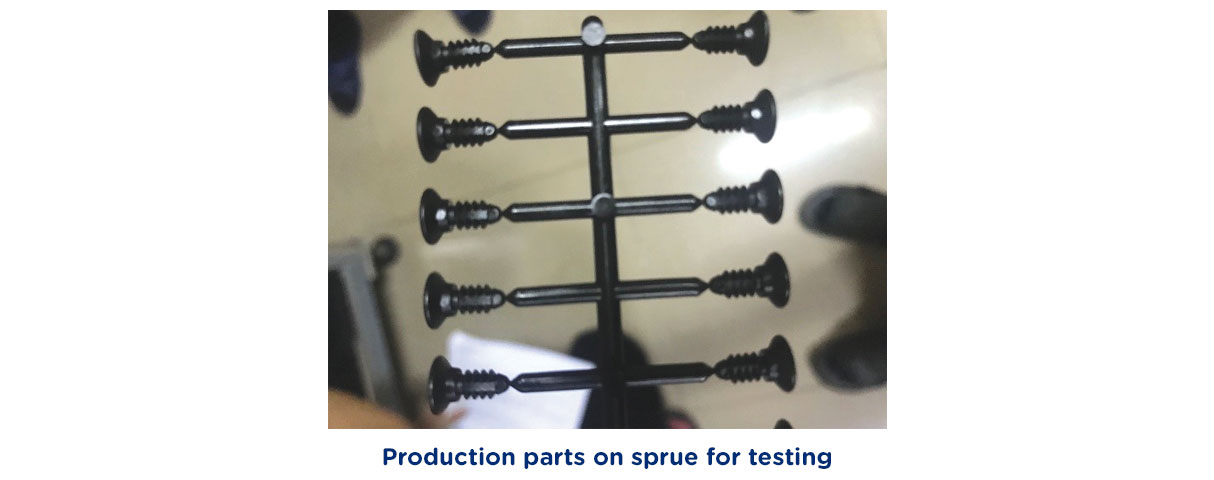
As part of the testing process, a formal audit partner was brought in, application tests including push in force, pull out force, individual cavity inspection, fail tests, shear strength testing, and others were all carried out.
"I invited the customer’s senior engineer who happened to be based only 30 mins away from our vendor’s factory in China. The plan was to show him the design process and summary to date, all of which was prepared in advance by our vendor for the day in question. We worked on their production line to see the final design running live and took samples from the line for inspection. Whilst this was being done, a team of engineers was busily conducting a full PPAP, which was presented in the afternoon. Upon asking the customer’s engineer for his decision he commented: ‘How can I possibly reject a presentation and product like this, I have never seen such an efficient, well prepared and executed product audit in all my years as an engineer’. At which point the green light was given
As a final deliberate destruction test as this product is unwrapped and assembled by the public for home use, he asked three of us to physically hold down the stand, at which point he put his foot against the desk and physically tore the PC bracket from the stand. Amazingly the metal stand snapped, but the four special plastic push screws remained firmly in place! At which point he simply smiled!”
Project challenges
The project required the design and manufacturing of a unique product, so this was both an exciting but challenging opportunity for the TR team. From the start, it required a lot of additional testing and resources that all partners needed to be involved with and had to collaborate closely together on.
In early design phase, it was a concern that the pull-out force required to remove the screw from above the unit would be too weak, so this needed addressing. The question was raised as to how additional tooling could be used to resize the existing part and modify it. In a short time, and through collaboration, this was improved and a sweet spot in the tightness of the shank was achieved, providing acceptable installation force, and enhanced pull out force.
Under normal usage testing, the rivet was pushed into the fixture TR had provided and removed using a standard screwdriver. This was repeated eight times then the insertion force of the 9th time pressing fixture and the pulling force when forced out. In wall mount passing test under the weight of 15.0KGF tested for 24 hours the screws remained tight in place.
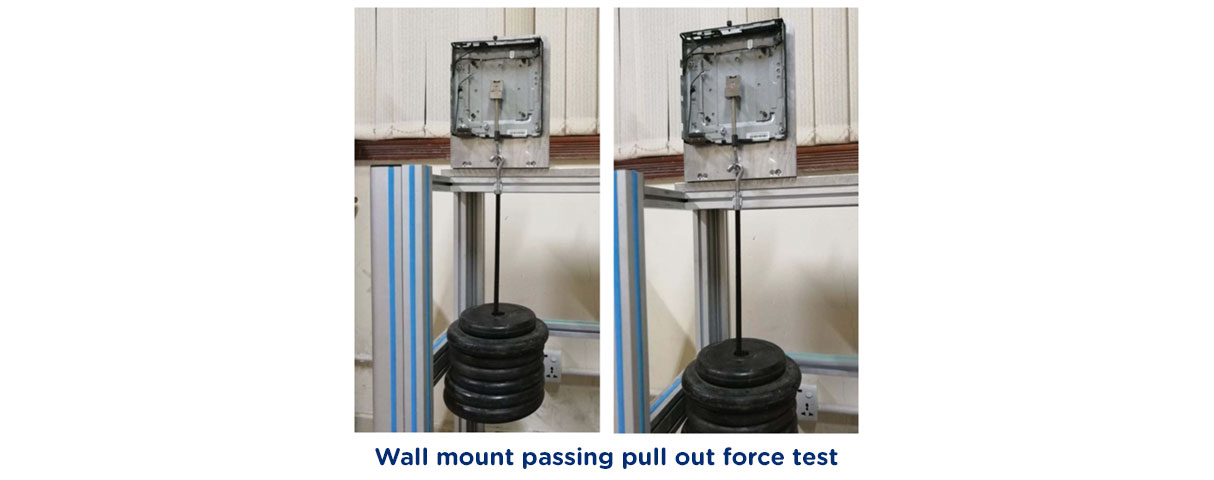
Project conclusion
TR Fastenings has developed a solution that is unlike anything currently on the market. It has the capability to be a game changer for the home computing market. It joins an entire range of M3-M8 sizes in three different head styles to suit a variety of applications.
The team at TR has worked to create a product that has the capability to change the way fasteners are used with PC screen brackets, delivering increased product life and enhanced quality.
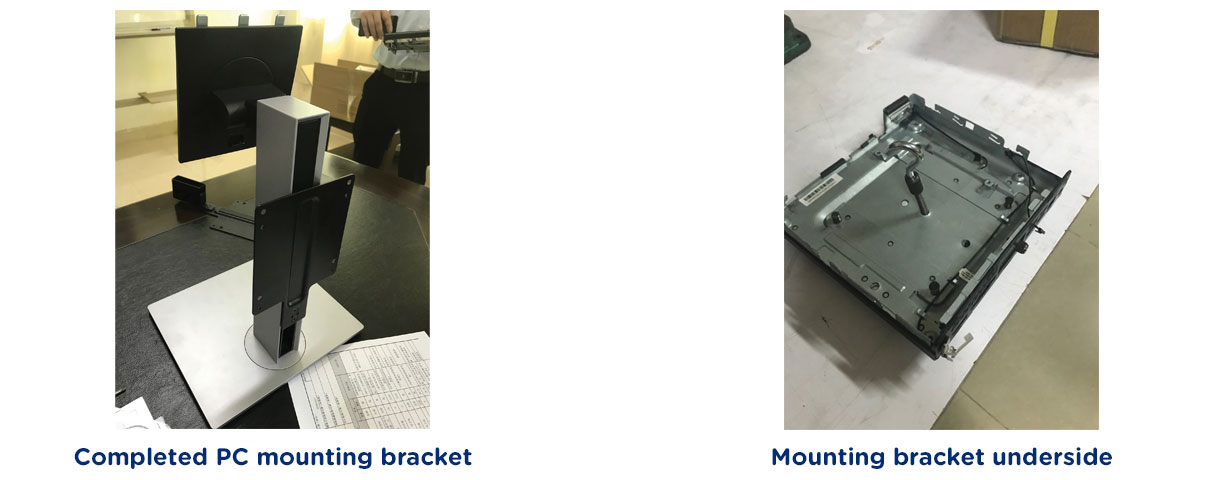
Related articles:
- Fastfixtechnology.com, Online, 10th July 2023: ‘TR Fastenings designs a unique push screw solution’
- Design Solutions, September 2023: 'Designing a Push Screw solutions for monitor mounting brackets'
- Fastener Eurasia, September 2023: 'TR Fastenings designs a unique push screw solutions for monitor mounting brackets'