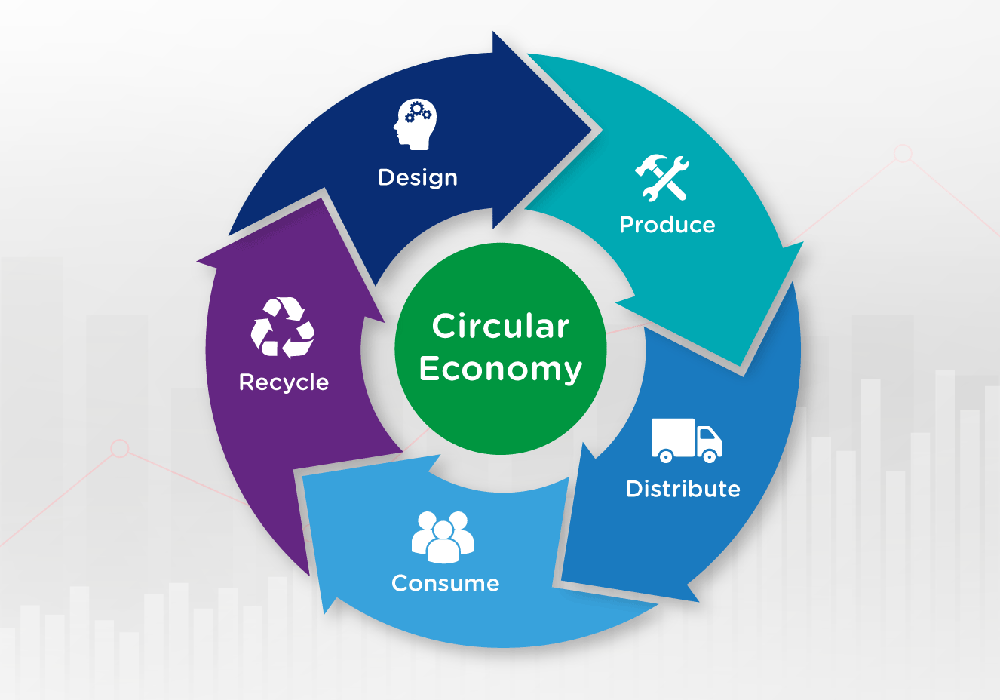
Design in a circular economy
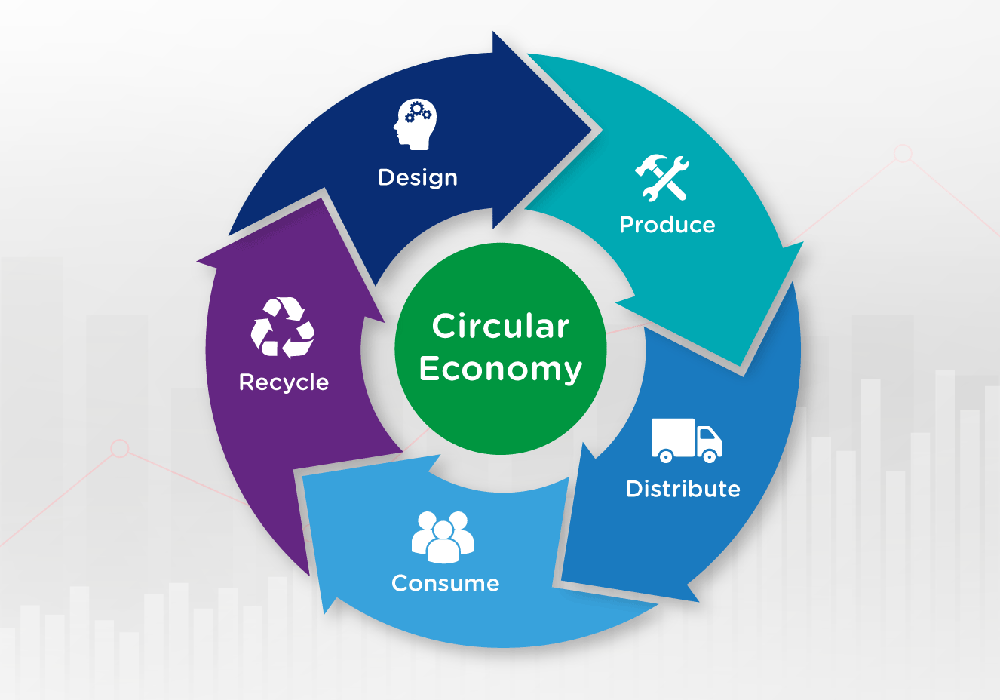
Design in a circular economy
Design for Manufacturing (DFM) and Design for Assembly (DFA) are the integration of product design and process planning into one common activity. The goal is to design a product that is easily and economically manufactured giving up-front cost-effective solutions.
Additionally, our Engineers promote the inclusion of the ability to reuse, repurpose or recycle into the design.
TR’s involvement is essential at the concept and prototype stages to ensure the correct choice of fastening methodology, assisting in achieving your carbon targets, whilst optimising your designs and products.
The horizon of innovation is changing continuously in the race to a more sustainable ecosystem, and various disruptive technologies in manufacturing have become mainstream. At TR we aim to stay ahead of the curve and embrace the use of new and mixed materials, electrostatic finishes and composites with a focus on non-ferrous products within the electrification of mobility, whilst respecting commercial requirements.
Design for recyclability
Fasteners generally account for less than 2% of the complete product weight. Recycling value streams are therefore formulated around the materials with the highest content, are the most valuable or are easiest to recover. Fasteners can play a major role in the efficiency of recovery of materials by either aiding removability or the potential of separation, for example:
- Products manufactured of homogenous plastics can be ground to provide raw material for the remanufacture of plastic components. The use of steel fasteners will allow these to be magnetically separated from the ground material, allowing both plastic and steel to be recycled
- Using fasteners of similar materials as the main structure allows these to become part of the recycled material. For example, with the correct choice of coating on aluminium or steel fasteners, this can increase the overall recyclability of your design and product
Design for assembly
Our fastener Engineers can provide support and guidance when taking a design from prototype into serial production. Selecting a common drive system provides tool flexibility within the assembly line, but also enables remote maintenance or disassembly units to use universal tools particularly in hostile environments.
Alternative drive systems or drive sizes can be applied to fulfil Poka-Yoke requirements during assembly and assist with field repair and maintenance.
Product line optimisation and automation often requires modifications on existing fasteners. Our experience in diverse applications and markets allows us to support you in making the right design decisions.
Design for manufacture
Having our own manufacturing locations gives us a wealth of engineering knowledge and experience which customers can utilise.
Our Engineers work on refining tool design, production processes and efficiencies. Feasibility Engineers make sure we comply with customer’s drawings and requirements to help identify any areas of concern or risk. Drawing on our expertise in developing products for high-volume production, we can provide advice on design and specification suited for the most economical manufacture.
End-to-End design
Our engineering team forms an integral part within the TR structure, working closely with all other teams to ensure a smooth transition from ideation and concept creation to prototyping and serial production. Sustainable design development criteria also references the inherent and consistent process and product quality and its documentation, such as PPAP or other approvals.