TR Self Clinch Broaching Standoff installation
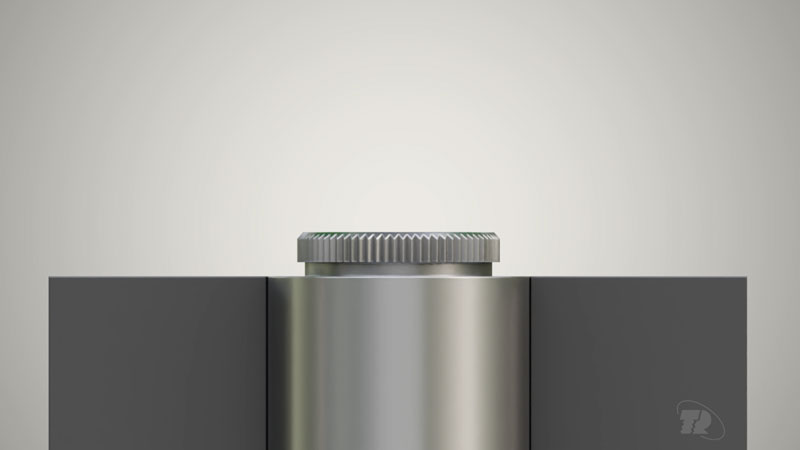
Select the appropriate hole size from the table below for the standoff size required. Punch the hole diameter into the sheet material.
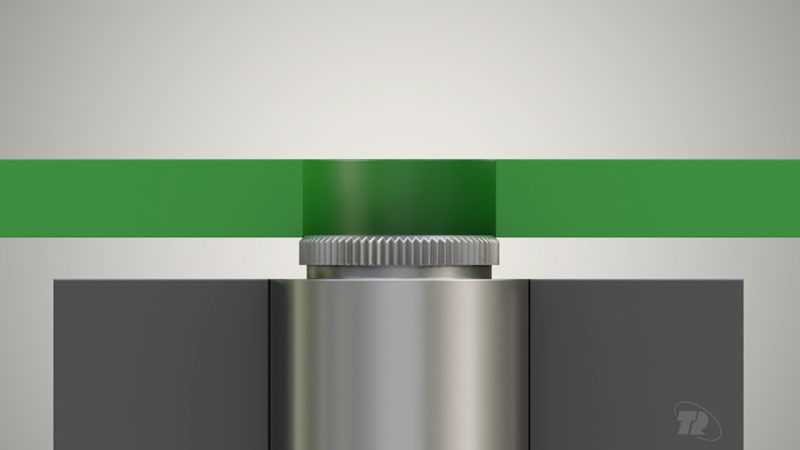
Place the standoff spigot end into the hole on the side opposite the mating face. So that standoff rests on the serrations. Ensure both plate and stand-off are aligned along the same axis. If the standoff is not seated ‘square’ in the hole, the joint will be imperfect and mating threads will misalign.
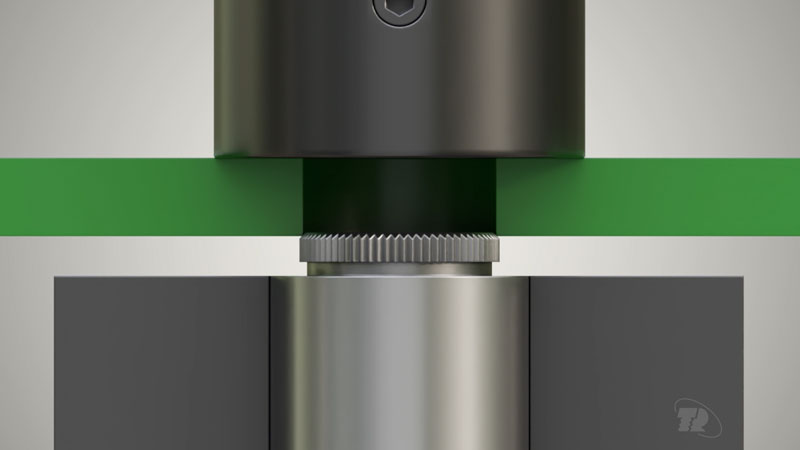
Using a profiled punch, apply only sufficient pressure to ‘squeeze’ the standoff serrations into the parent sheet metal.
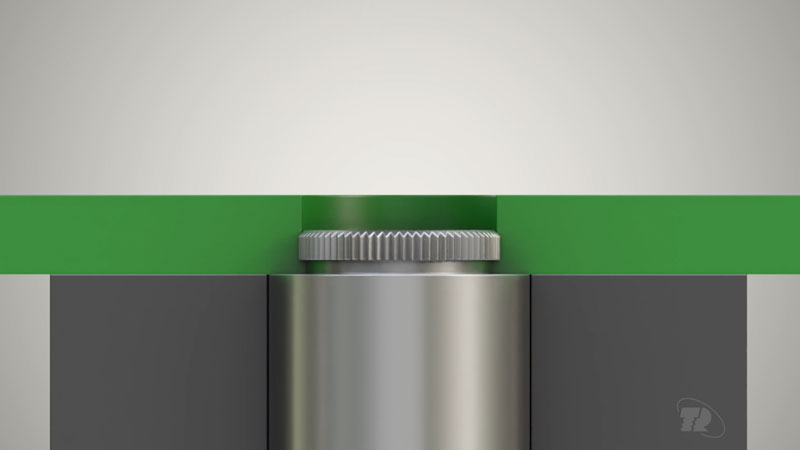
The serrations if properly installed will provide torsional (rotational) resistance. After installation the spigot joint should be flush with the sheet metal.
Installation animation
Using the table below with reference to the specific size of the Broaching Standoff, select the correct hole size for the installation of the fastener.
For the best dimensional accuracy and therefore performance, TR Fastenings recommends that all holes in the sheet metal application be punched.
Note it is essential that the recommended hole tolerances be observed.
Hole sizes - metric (mm)
Thread or through hole size | M2.5 | M3 | M4 | 3.6 | 4.2 |
---|---|---|---|---|---|
Minimum rec sheet thickness | 1.53 | 1.53 | 1.53 | 1.53 | 1.53 |
Hole size +0.08 -0.00 | 4.22 | 4.22 | 6.4 | 5.4 | 6.4 |
Minimum distance to edge of sheet | 4.4 | 4.4 | 6.4 | 5.5 | 7 |
Hole sizes - inches
Thread or through hole size | 4-40 | 6-32 | 0.116 | 0.143 |
---|---|---|---|---|
Minimum rec sheet thickness | 0.06 | 0.06 | 0.06 | 0.06 |
Hole size In sheet + 0.003 - 0.000 | 0.166 | 0.213 | 0.166 | 0.213 |
Minimum distance to edge of sheet | 0.17 | 0.22 | 0.17 | 0.22 |
Tooling
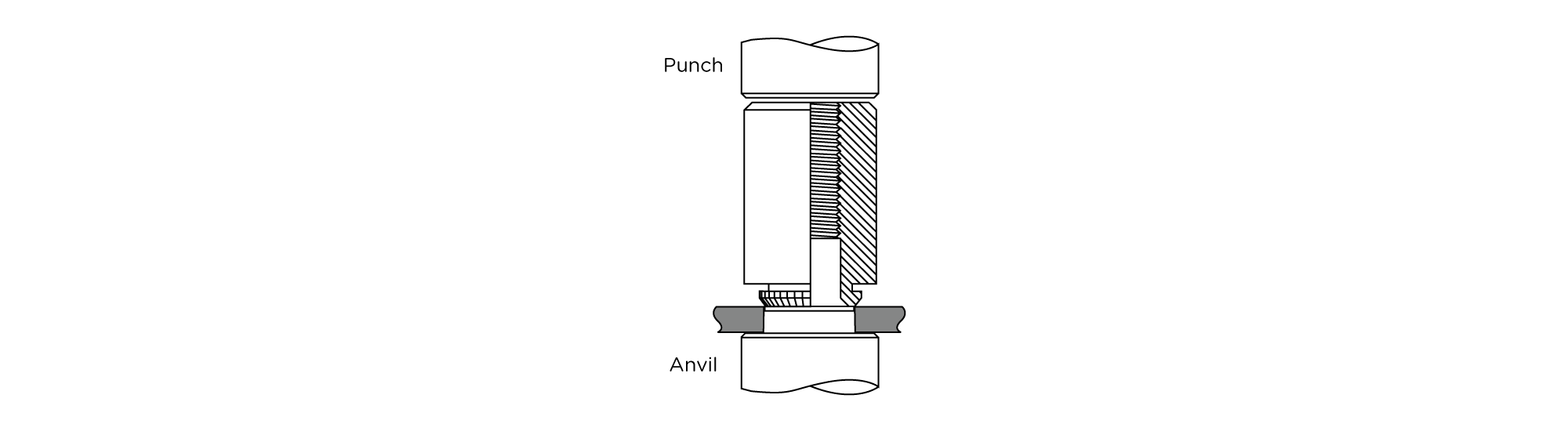