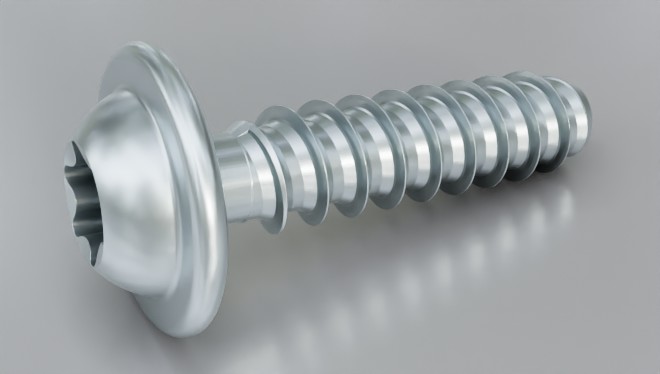
Flange Head
This article provides technical information for the high performance Plas-Tech 30-20® screws for plastics.
The Plas-Tech 30-20® is the high-performance fastener within the TR Fastenings range of screws for plastic. It is highly versatile for high load applications in a wide range of thermoplastics, composites, aluminium and magnesium.
The market leading thread design, already adopted and specified for many applications in the automotive and home appliances markets, accommodates high loads because of its optimised material flow during installation enabling a higher clamp load.
![]() |
The thread profile consists of several distinctly angled surfaces. The 30-degree tip of the thread provides a strong and reliable edge, increasing the cross-sectional thickness of the 20-degree flanks for more axial strength. These 20-degree flanks are optimised for optimum load transfer between the plastic and screw. The base of the thread consists of 140-degree flanks to optimise material flow during installation.
|
Features | Benefits | Compared to conventional thread forming screw |
---|---|---|
Optimal thread pitch, combining performance and fast installation, suitable for robotic installation | The optimised thread pitch ensures a high axial shear plane between the threads, whilst ensuring fastener engagement with a minimum number of rotations, keeping installation times to a minimum. The Hexalobular drive avoids camming out | The Plas-Tech 30-20® has a 20% finer pitch, reducing the thread angle. Together with the lower flank angle and optimised material flow, axial resistance has improved substantially |
Compliant with the ‘Design to Repair’ principle | The fastener can be removed and installed numerous times, because of limited damage to the formed thread in the plastic during retightening. The joint therefore maintains its integrity | The reduced thread angle reduces axial displacement when tightening with a focus on axial loading |
Optimal material flow into plastic | Stronger, reliable, and consistent joints with a higher pre-load can be achieved through optimised material flow between the threads, creating maximum shear strength | A 25% higher thread fill with an overall larger cross section, improves maximum joint strength and resistance against loosening caused by vibration |
Reduced radial stress in plastics | Reliable and repeatable joints are created by the multi angled thread profile, directing the plastic in axial direction, thereby reducing the radial stress. Plas-Tech 30-20® can eliminate the need for threaded inserts | The narrower thread shape forms the plastic, with reduced radial stress. The 30⁰ crest of the thread and the 20⁰ flank combines screw strength with maximum axial joint loading capacity |
Superior vibration resistance against loosening | The full engagement of the self-locking, angled thread design avoids loosening due to vibration | The Plas-Tech 30-20® reduced thread angle, and optimised material flow during installation increase vibration resistance in applications |
High torsional and tensile strength of the fastener | A large core thread profile reduces the risk of sudden screw failure | A 20-25% increased core diameter ensures superior torsional and axial strength |
Symmetrical thread profile | The symmetrical thread profile in both products provides a high fatigue strength and breaking torque | The symmetrical thread profile in both products provide a high fatigue strength and breaking torque |
Full thread consistent thread profile with a convex tip | The high consistency of the thread profile allows rationalisation of fastener lengths. The convex edge increases the strength of the thread against damage prior to installation, allowing thinner and shorter boss designs | The overall higher performance of the fastener and causing relative lower radial stress in its joining material, reduction of screw sizes can aid rationalisation |
Other head styles, lengths, diameters, and materials are available upon application. The Plas-Tech 30-20® thread feature can also be applied to other engineered products, such as clinching studs, double ended studs, etc. Our engineering team at TR Fastenings can support you with the design and guidance on the application.
The mating part with the clearance hole is placed in position onto the plastic component which has a correctly sized moulded tapered hole.
The Plas-Tech 30-20® is placed in the hole and screwed in at the recommended speed. They are ideally installed with a calibrated electric driver and are particularly suited for automated robotic assembly systems. The tightening torque should be set correctly to ensure the appropriate clamp load.
As the screw drives in and the threads displace the surrounding plastic, the displaced plastic flows into the core of the screw forming an internal thread. The profile thread is designed to reduce radial stress and the potential damage of the surrounding plastic.
The Plas-Tech 30-20® has been designed to install into ductile thermoplastics with a straight or tapered hole which have a typical diameter of 80% of the nominal diameter of the fastener. For stiffer and reinforced materials, it is recommended to increase the boss ID. This can be increased up to 88% of the nominal diameter.
The Plas-Tech 30-20® is suitable to install in dedicated moulded bosses, similar to other products in the Plas-Tech® range, the boss can be equipped with a 1-2⁰ draft angle to improve die release during moulding. To reduce local stresses near the top of the boss when in contact with mating elements, a counterbore can be applied.
The fastener design is based on a typical depth of thread engagement of twice the screw diameter. This to ensure that sufficient contact is made between the thread and plastic boss material. In stiffer and less ductile plastics it can be possible to reduce the thread engagement, whereas softer and more ductile plastics can benefit from an increased depth of engagement. It is recommended to test for the optimum hole diameter and thread engagement.
![]() |
Joint performance is a collaboration of the Plas-Tech 30-20® fastener, the boss material, and its design, together with the installation torque. A longer or larger screw does not always provide a better joint. Increased thread engagement requires a higher installation torque, which can lead to raised stresses in the boss material. Typically, a boss can be designed with a minimal outer diameter of twice the nominal diameter of the fastener. The boss diameter must be sufficient to resist damage during installation or through aging of the plastic. Physical testing of a joint is always recommended. |
Feature | Description | Guidance | Nominal value [mm]* | ||||
---|---|---|---|---|---|---|---|
Ød | Diameter of screw | - | 3 | 3.5 | 4 | 5 | 6 |
ØA | Inner Diameter of boss | 0.8d | 2.4 | 2.8 | 3.2 | 4 | 4.8 |
ØB | Outer Diameter of boss | 2d | 6 | 7 | 8 | 10 | 12 |
C | Minimum depth of engagement | 2d | 6 | 7 | 8 | 10 | 12 |
Ø Counterbore | Diameter of counterbore | d+0.2 | 3.2 | 3.7 | 4.2 | 5.2 | 6.2 |
Depth Counterbore | Depth of counterbore | 0.4d | 1.2 | 1.4 | 1.6 | 2.0 | 2.4 |
Draft Angle | Draft Angle inner Diameter of boss | - | 1-2⁰ |
A secure joint is achieved through a full installation of the screw with sufficient pre-load. Keeping the tightening torque to a minimum, effects of creep or risk of stripping thread are reduced.
For serial installation, it is typically safe to consider a tightening torque between the installation and stripping torque, according to Tserial = (25 x Tstrip + 75 x Tinstallation)/100. This should avoid thread stripping, whilst providing sufficient pre-load upon achieving full installation of the screw.
The optimum tightening torque is based on a range of variables, including installation speed, boss material and the joint design. Very high installation speeds can have negative effects on the joint assembly, not allowing the mating plastic sufficient time to equalise and distribute stress. 400 RPM free running speed accommodates most materials and can be taken as an initial setting.
Test undertaken at TR Fastenings' Technical and Innovation Centre show direct correlation between hole diameter, and the respective installation and stripping torques. By determining the lowest stripping-installation ratio an indication of the optimal hole diameter can then be established. Below is a graph of a typical application result in a straight hole just below 80%, for a 4mm Plas-Tech 30-20® in extruded Polyamide 6.6 GF30, using a tool with a free running speed of 400 rpm.